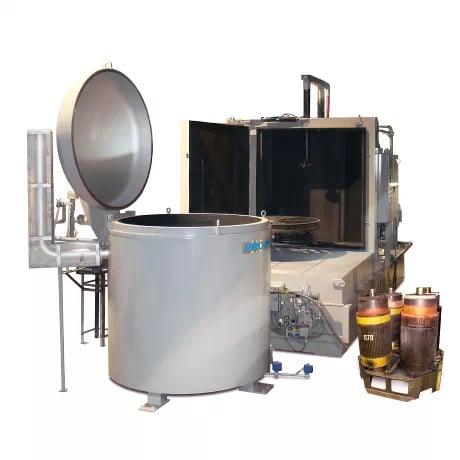
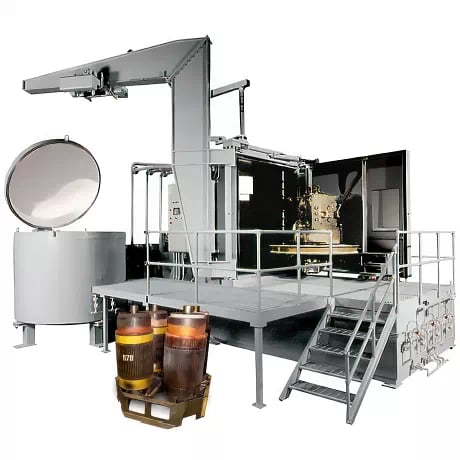
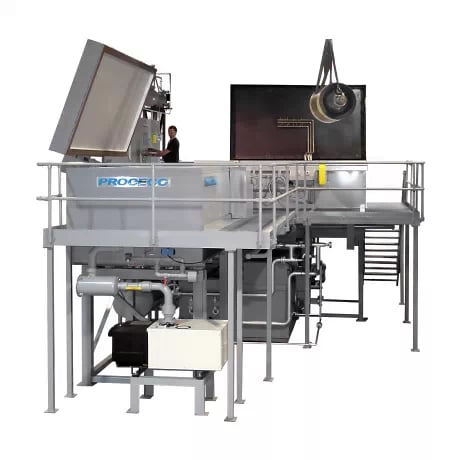
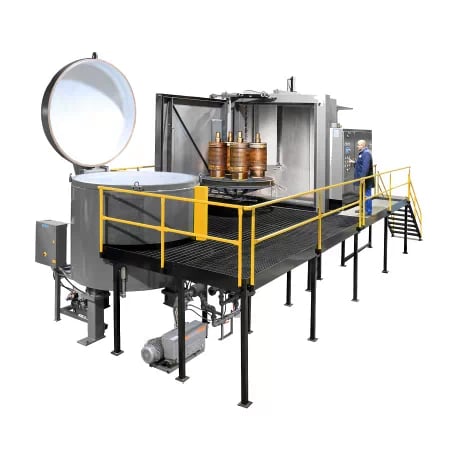
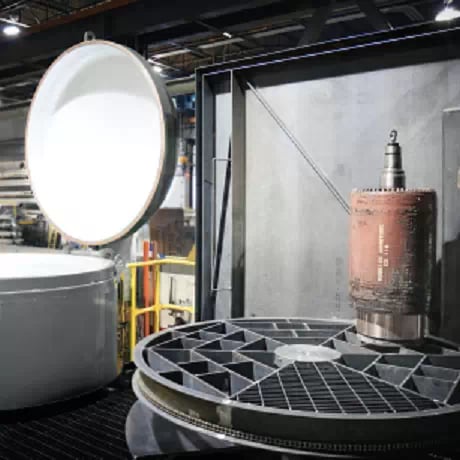
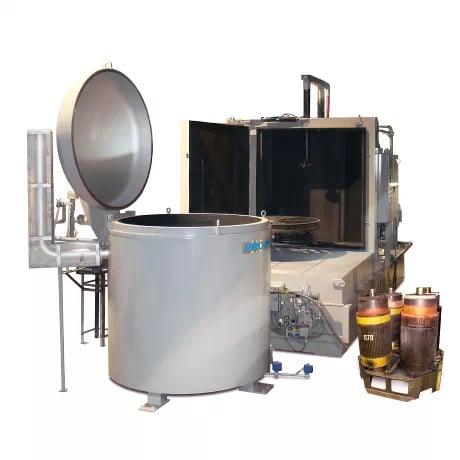
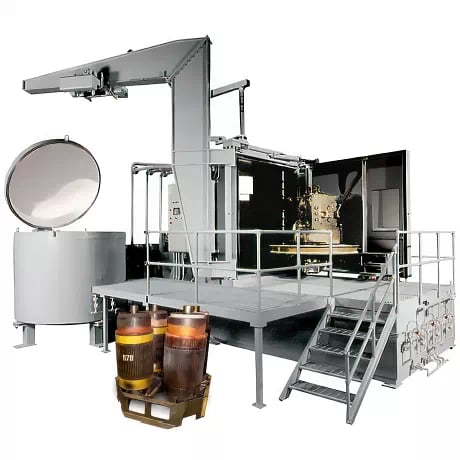
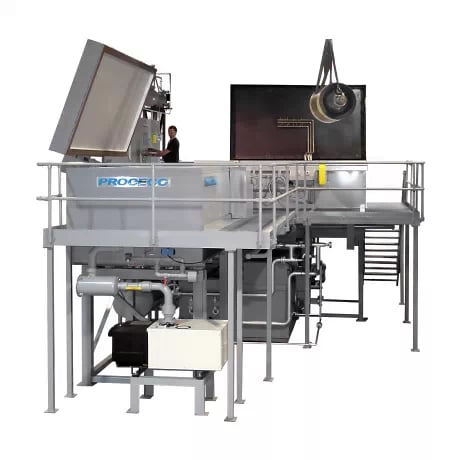
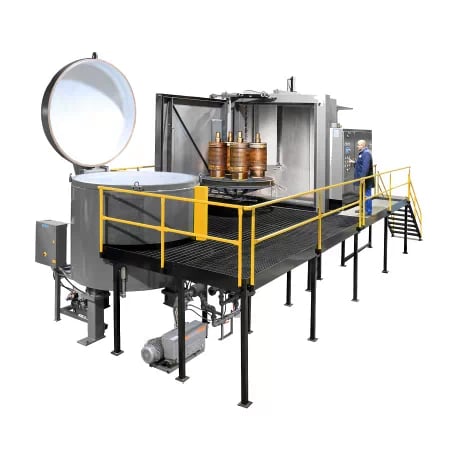
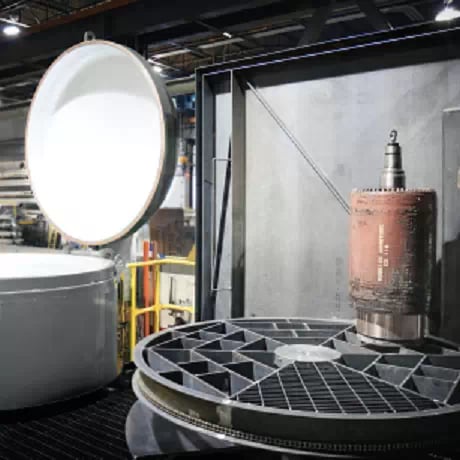
Traction Motor Cleaning and Vacuum Drying Station
Key benefits
- Proven choice of rebuilders worldwide for traction motor cleaning
- Environmentally safe—heavy-duty, fully automatic degreasing process
- Effectively removes oil, grease, and road dirt
- Full high-flow spray coverage of motor interior and exterior
- 3-stage fully recirculating wash process effectively rinses-off detergent residue, resulting in fewer rejects
- Vacuum dryer features low-energy principle to completely dry — deep inside the windings
Overview
As a key partner to the rail and transit industry, PROCECO has helped modernize maintenance depot parts cleaning operations, replacing harmful chemicals and manual processes with environmentally friendly, automatic degreasing equipment. All of our cleaning technology uses water-based cleaning solutions instead of harmful solvents. During the wash cycle, workpieces are sprayed with recirculated, hot aqueous solution containing a low detergent concentration (between 2% and 5%) to effectively remove oil, greases, and road dirt prior to rebuilding processes.
During the overhaul of traction motors (TMs) the first and most important operation is the perfect cleaning and drying of stator and rotor windings, prior to testing and diagnostics. Poor cleaning, rinsing and drying will cause:
- False diagnostic test readings leading to unnecessary rewinding operations.
- Residual dirt and carbon dust on stators and rotors that will contaminate varnish tanks.
- Residual detergent left in windings after cleaning that will deteriorate insulation and attract humidity, all of which will lead to premature motor failures.
- Specification sheets
- Download resources
- Videos
TESTIMONIALS
The washer and vacuum dryer provide excellent and efficient component cleaning and drying. They are user-friendly, requiring minimal supervision during operation. Additionally, the machine demands low maintenance, with upkeep tasks being straightforward. Technical support has also been reliable and helpful. [...] We are highly satisfied with the machine and would recommend it to companies considering a similar purchase.
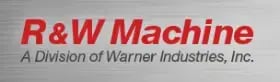
David Hnatovic
Vice President & General Manager
CONTACT A SOLUTION EXPERT
PROCECO develops aqueous cleaning systems that go beyond cleaning, by seamlessly integrating a wide range of processes and features that dramatically improve your productivity and profitability.